Understanding the Role of a Die Casting Parts Supplier
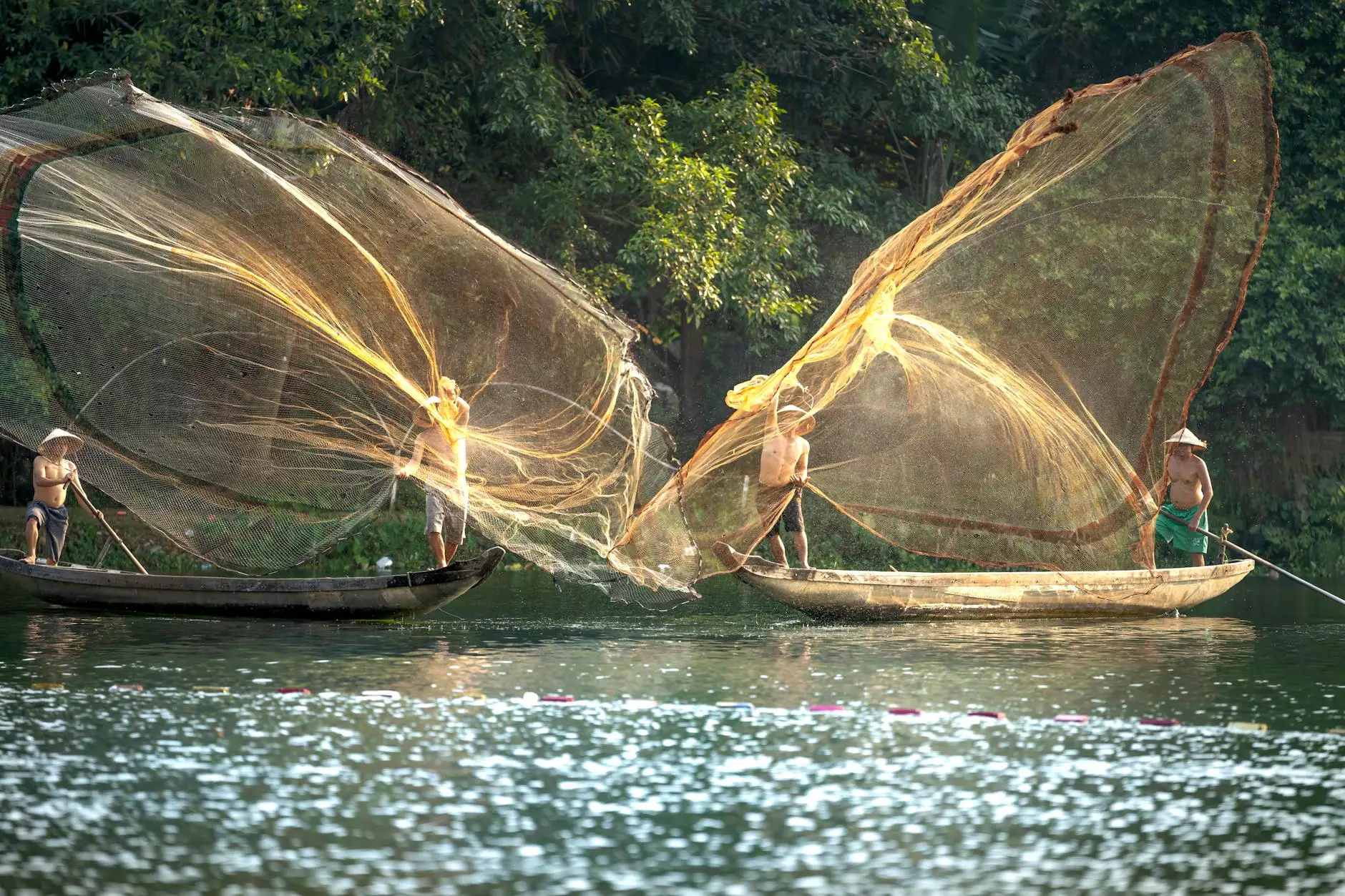
Die casting is a manufacturing process that allows for the creation of high-precision metal parts. As a crucial element within several industries, the role of a die casting parts supplier cannot be overstated. At Deep Mould, we focus on delivering top-quality die cast components that meet the diverse needs of our clients. In this article, we will explore the die casting process, its applications, and how selecting the right supplier can make a significant difference in your production quality.
What is Die Casting?
Die casting is a process that involves forcing molten metal into a mold cavity under high pressure. This method is ideal for producing a wide range of complex shapes and designs with excellent dimensional accuracy and surface finish. Some common die casting materials include:
- Zinc: Known for its excellent corrosion resistance and suitability for detailed geometries.
- Aluminum: Lightweight and strong, making it ideal for aerospace and automotive applications.
- Magnesium: Offers superior strength-to-weight ratios, frequently used in electronic housings.
- Copper: Preferred for electrical applications due to its high conductivity.
The Advantages of Die Casting
The die casting process offers numerous benefits, making it a favored choice among manufacturers. Here are some of the key advantages:
- High-Speed Production: Die casting is a rapid manufacturing method that allows for the mass production of parts.
- Excellent Precision: The process ensures tight tolerances, greatly reducing the need for secondary machining.
- Complex Geometries: Die casting can produce complex shapes that would be difficult or impossible to achieve with traditional manufacturing methods.
- Quality Surface Finish: Components produced via die casting exhibit a superior surface finish, reducing the need for additional treatments.
Industries Benefiting from Die Casting
Many industries leverage the advantages of die casting. Let’s take a closer look at a few of these sectors:
Aerospace
The aerospace sector requires components that are lightweight yet incredibly strong. Die casting provides solutions that meet these demanding specifications, ensuring safety and performance in flight.
Automotive
In the automotive industry, die casting is utilized to produce various components, including engine blocks, transmission cases, and structural parts. The ability to design parts that withstand heavy stress while being lightweight is crucial for fuel efficiency and performance.
Electronics
Electronics manufacturing benefits from die casting through the creation of housings and heat sinks. The conductivity of metal materials aids in effective heat dissipation, keeping electronic devices running smoothly.
Consumer Goods
From small appliances to intricate home decor items, die casting allows manufacturers to create aesthetically appealing products with functional durability. Many consumer products rely on die-cast metal for both form and function.
Selecting the Right Die Casting Parts Supplier
Choosing the right die casting parts supplier is essential for ensuring the quality and reliability of your components. Here are some factors to consider when making your selection:
Experience and Expertise
The supplier’s experience within the industry is critical. Companies such as Deep Mould, with years of specialized knowledge, can provide insights that less experienced suppliers may not offer.
Quality Assurance
It's vital to inquire about the quality control measures the supplier has in place. High-quality die casting requires stringent adherence to specifications and standards. Look for suppliers with ISO certification or similar quality management systems.
Technical Capabilities
Assess the technical capabilities of your potential die casting parts supplier. A supplier with advanced equipment and technology will likely deliver superior products and custom solutions tailored to your needs.
Material Selection
Verify that the supplier offers a range of materials to meet your project requirements. Different applications may call for specific metals and alloys, so a diverse supplier can ensure you receive the best materials for your needs.
Customer Support
Quality customer support can differentiate a great supplier from a mediocre one. Look for suppliers who provide dedicated account managers and are responsive to your inquiries throughout the project lifecycle.
The Die Casting Process at Deep Mould
At Deep Mould, we adhere to a systematic approach for our die casting operations, ensuring precision and quality in every component we manufacture:
- Design Phase: Collaborating closely with clients to understand their requirements and create detailed designs.
- Tooling Development: Designing and building high-quality molds that allow for efficient production.
- Melting and Pouring: Melting metal to the appropriate temperature and pouring it into the molds under pressure.
- Cooling: Allowing adequate cooling time for the metal to solidify and retain its shape.
- Trimming and Finishing: Cutting excess material and finishing the parts to meet aesthetic and functional requirements.
- Quality Control: Conducting rigorous inspections to guarantee the highest level of quality and precision.
Conclusion
In conclusion, the significance of selecting a trusted die casting parts supplier, such as Deep Mould, plays a crucial role in enhancing your manufacturing capabilities. With the right expertise and technology, die casting can effectively meet the complex demands of modern industries. Whether you need parts for the aerospace, automotive, electronics, or consumer goods sectors, investing in quality die casting components is essential for success.
Explore our range of services and discover how we can assist you in achieving your production goals. For high-quality die casting solutions and unparalleled customer service, consider partnering with Deep Mould today.