Exploring Precision Mold Parts in Metal Fabrication
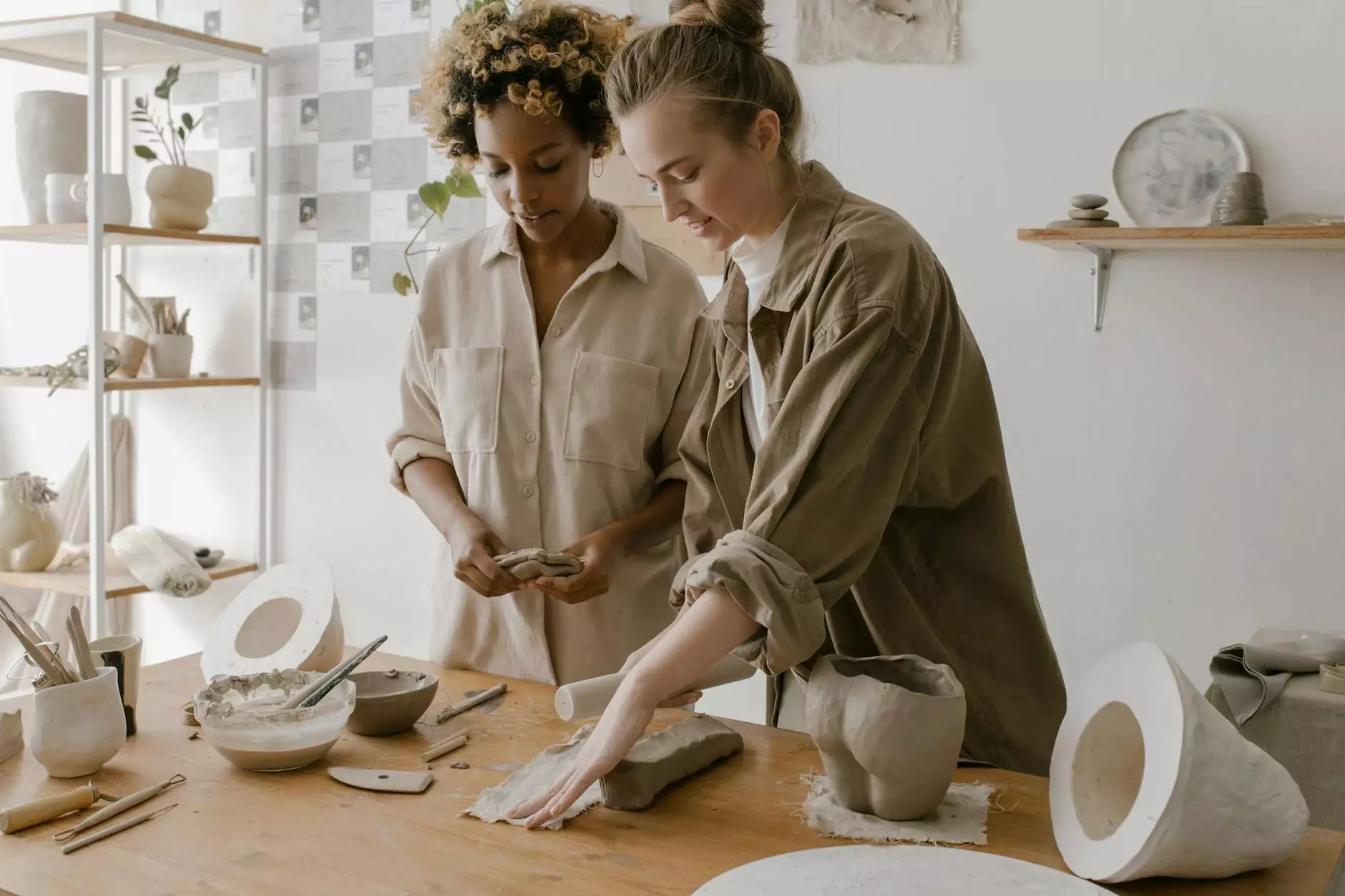
In the world of metal fabrication, the significance of precision mold parts cannot be overstated. These components are essential not only for ensuring quality and consistency but also for maximizing efficiency in the manufacturing process. As industries evolve and demand for precision increases, understanding the intricacies surrounding precision mold parts becomes imperative for businesses looking to thrive.
The Role of Precision Mold Parts in Manufacturing
Precision mold parts are integral to the production of various products across multiple industries. They serve as the foundation for molding processes, allowing manufacturers to achieve high levels of accuracy and repeatability. Whether it’s for automotive parts, consumer products, or industrial equipment, the reliability of precision mold parts directly influences the overall quality of the final product.
Key Functions of Precision Mold Parts
- Shaping Products: Precision molds are designed to shape materials into desired forms, ensuring that every product meets strict dimensional tolerances.
- Consistency: Utilizing precision mold parts guarantees consistency across batches, which is essential for quality assurance.
- Cost Efficiency: Accurate molds reduce material waste and minimize production errors, resulting in significant cost savings for manufacturers.
- Complex Designs: Precision molds allow for the creation of intricate designs that would be impossible to achieve through traditional methods.
The Benefits of Using Precision Mold Parts
Incorporating precision mold parts in the manufacturing process offers a wide array of benefits. Understanding these advantages can help business owners make informed decisions when selecting their manufacturing techniques.
1. Enhanced Product Quality
Products created with precision molds are known for their high quality. The accuracy that these molds provide means that the end product aligns perfectly with design specifications, reducing the risk of defects.
2. Increased Production Speed
The efficiency of precision molds allows for faster production cycles. Manufacturers can produce large quantities of parts in a shorter time frame, increasing overall productivity.
3. Flexibility in Design
Modern precision molds can accommodate complex geometries and intricate design requirements, offering businesses the flexibility to innovate and differentiate their products in the marketplace.
4. Reduced Labor Costs
Automating the mold-making process means fewer workers are needed on the production line, lowering labor costs while enhancing productivity.
5. Sustainability
By reducing material waste and optimizing the use of resources, precision molds contribute to more sustainable manufacturing practices, aligning with the growing demand for environmentally friendly production methods.
Applications of Precision Mold Parts
From automotive components to household appliances, the applications of precision mold parts are vast and varied. Here are some key areas where they are prominently utilized:
1. Automotive Industry
The automotive sector relies heavily on precision mold parts for manufacturing everything from engine components to interior fixtures. The demand for lightweight and high-strength materials necessitates the use of precision molds to ensure each part meets rigorous safety and performance standards.
2. Medical Devices
In the medical field, where accuracy and reliability are paramount, precision mold parts play a critical role. Manufacturers of medical devices use molds to create components that are not only precise but also compliant with strict regulatory standards.
3. Consumer Electronics
With the rise of technology, the consumer electronics industry has seen an increased demand for precision molding. High-quality mold parts ensure that components fit together seamlessly, enhancing the overall user experience.
4. Aerospace Components
The aerospace industry demands the highest levels of precision due to safety regulations and performance specifications. Precision mold parts are crucial in producing lightweight and durable parts that can withstand extreme conditions.
Choosing the Right Precision Mold Parts Manufacturer
When it comes to sourcing precision mold parts, selecting the right manufacturer is essential. Here are some factors to consider:
1. Experience and Expertise
It's crucial to choose a manufacturer with a proven track record. Look for companies that specialize in precision molding and have extensive experience in your specific industry.
2. Technology and Equipment
Assess the technology and equipment used by the manufacturer. Advanced CNC machines and CAD software indicate a commitment to precision and quality.
3. Quality Assurance Processes
Investigate the manufacturer's quality assurance processes. A robust quality management system should be in place to ensure that every part meets strict specifications.
4. Customer Support
Effective communication and support are vital. A good manufacturer should be willing to work with you through all stages of the project, from design to delivery.
The Future of Precision Mold Parts in Metal Fabrication
The future of precision mold parts looks promising as technology continues to advance. Innovations such as 3D printing and smart manufacturing are set to revolutionize the industry, further enhancing the capabilities and applications of precision molding. As businesses look for competitive advantages, those that invest in high-quality precision mold parts will undoubtedly stand out in the market.
Conclusion
In conclusion, precision mold parts are a cornerstone of modern metal fabrication, driving efficiency, quality, and innovation across various industries. By understanding their role and the multitude of benefits they offer, manufacturers can enhance their production processes and ultimately lead to greater business success. As the demand for precision continues to grow, investing in quality precision mold parts should be a top priority for forward-thinking businesses. To learn more about how precision mold parts can elevate your manufacturing process, visit deepmould.net.