Silicone Injection Molding: Revolutionizing Electronics and Medical Supplies
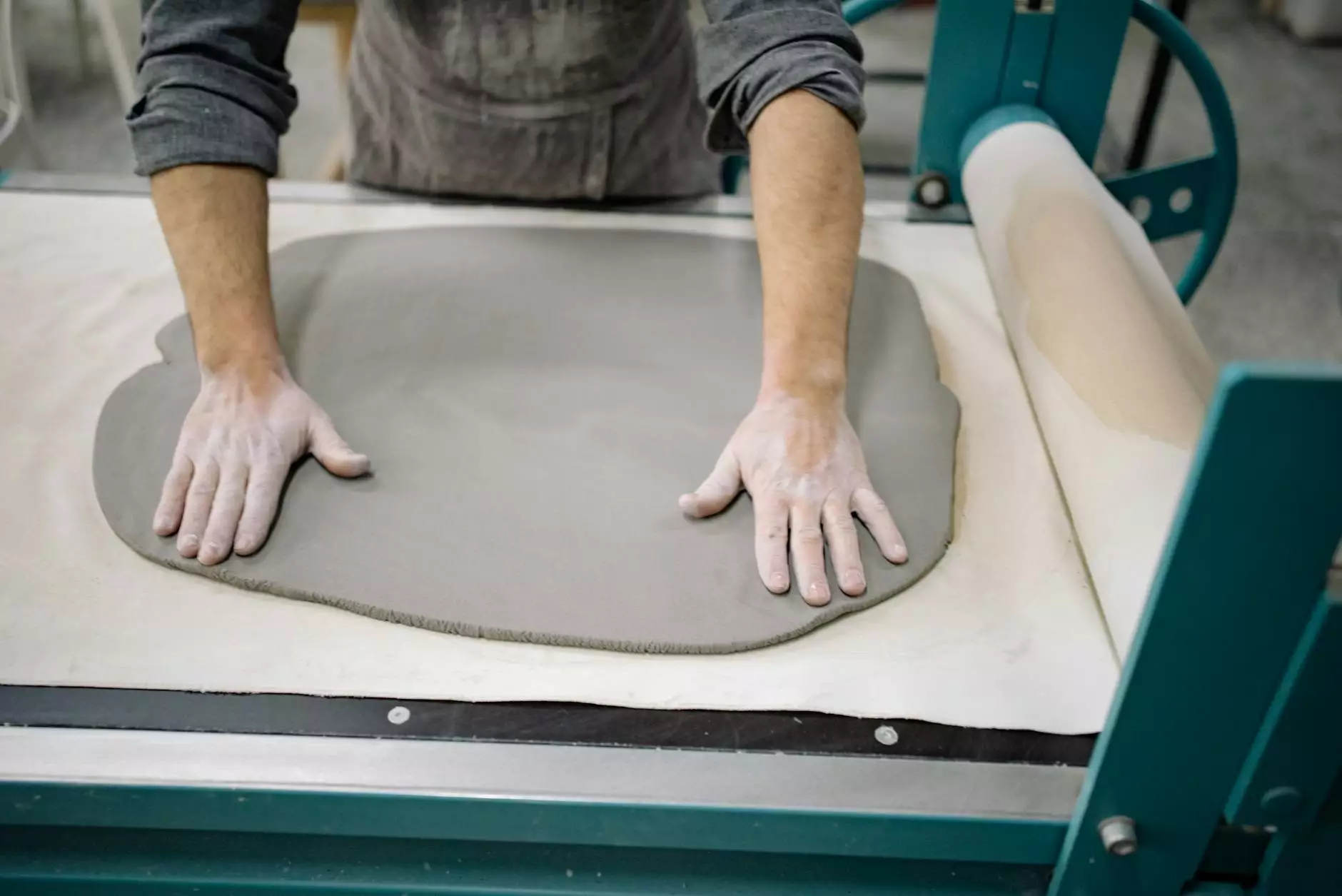
Silicone injection molding is a cutting-edge manufacturing process that has gained traction in various industries, particularly in electronics and medical supplies. This article delves deep into the processes involved, the unique advantages it offers, its vast applications, and its future in these vital sectors.
Understanding Silicone Injection Molding
At its core, silicone injection molding is a technique used to produce silicone rubber products by injecting liquid silicone rubber (LSR) into a mold. The process involves several key steps:
- Preparation of Materials: Liquid silicone and optional additives are mixed to achieve the desired properties.
- Injection: The mixture is injected into a precisely designed mold under high pressure.
- Curing: The material undergoes heat curing, allowing it to solidify into the desired shape.
- Cooling: After the curing phase, the newly formed component is cooled to ensure stability.
- Ejection: Finally, the mold is opened, and the finished product is ejected.
Benefits of Silicone Injection Molding
The remarkable benefits of silicone injection molding make it a preferred choice for manufacturers in the electronics and medical fields:
1. Exceptional Versatility
Silicone can be formulated to achieve a wide range of properties—from soft and flexible to firm and durable. This versatility allows manufacturers to develop customized products tailored to specific application requirements.
2. Superior Durability
One of the standout features of silicone rubber is its excellent resistance to extreme temperatures, UV exposure, and chemical degradation. Products made from silicone boast a longer lifespan, reducing the need for frequent replacements.
3. Biocompatibility
For the medical supplies industry, biocompatibility is crucial. Silicone meets stringent regulations regarding safety and is non-toxic, making it perfect for applications in medical devices and implants.
4. Precision and Efficiency
The injection molding process allows for high precision in manufacturing, ensuring even complex designs can be accurately replicated. This leads to decreased waste and more efficient production runs.
5. Cost-Effectiveness
The high-speed nature of silicone injection molding, coupled with reduced material waste, results in significant cost savings—making it an attractive option for high-volume manufacturing.
Applications in Electronics
In the electronics industry, silicone injection molding is employed in various applications:
1. Seals and Gaskets
Silicone’s excellent sealing properties make it ideal for creating durable seals and gaskets that protect sensitive electronic components from moisture and dust.
2. Keypads and Switches
Manufacturers often utilize silicone for producing soft-touch keypads. The material's tactile properties enhance user experience while ensuring durability against wear and tear.
3. Encapsulation
When it comes to protecting electronic components, silicone injection molding is used for encapsulating circuit boards. This process safeguards against environmental exposure and mechanical stresses.
4. Connectors and Housings
Due to its high resistance to temperatures and chemicals, silicone is used for connectors and housings in various electronic devices, enhancing their longevity.
Applications in Medical Supplies
The medical supplies industry also benefits immensely from silicone injection molding through various applications:
1. Catheters
Silicone catheters are extensively used due to their flexibility and biocompatibility, making them safe for prolonged use in the human body.
2. Surgical Instruments
Silicone components are integrated into many surgical instruments for their non-reactive properties, enhancing patient safety and comfort.
3. Medical Device Housings
Many electronic medical devices utilize silicone enclosures, offering protection while enabling easy cleaning and maintenance.
4. Prosthetics and Implants
The softness and pliability of silicone make it an ideal choice for prosthetics and implants, providing comfort and flexibility to users.
Future Trends in Silicone Injection Molding
The landscape of silicone injection molding is rapidly evolving, driven by technological advancements and increasing demand for innovative solutions. Here are some future trends worth noting:
1. Smart Silicone Products
As the Internet of Things (IoT) expands, the integration of smart technology within silicone products is on the rise. Manufacturers are exploring ways to embed sensors and connectivity directly into silicone components.
2. Sustainable Practices
Environmental concerns are shaping the future of manufacturing. Companies are investing in sustainable practices, including using recycled silicone and reducing energy consumption during the molding process.
3. Advanced Manufacturing Techniques
Technological advancements such as 3D printing and automation are set to enhance the capabilities of silicone injection molding, enabling faster prototyping and production runs.
4. Regulatory Changes
As industries evolve, so do regulatory frameworks. Manufacturers must stay abreast of changes concerning material safety and compliance to ensure their silicone products meet evolving standards.
Conclusion
Silicone injection molding stands at the forefront of modern manufacturing, particularly in the electronics and medical supplies sectors. Its unique advantages—ranging from durability and biocompatibility to cost-effectiveness—make it an invaluable method for producing high-quality products. As technology continues to evolve and industries demand more innovative solutions, silicone injection molding will undoubtedly play a pivotal role in shaping the future of manufacturing.
To learn more about how silicone injection molding can transform your manufacturing processes and enhance product quality, visit Nolato.com for more information. Embrace the future of production and discover the possibilities that silicone can offer across various industries!