The Transformative Power of Rapid Prototyping in Metal Fabrication
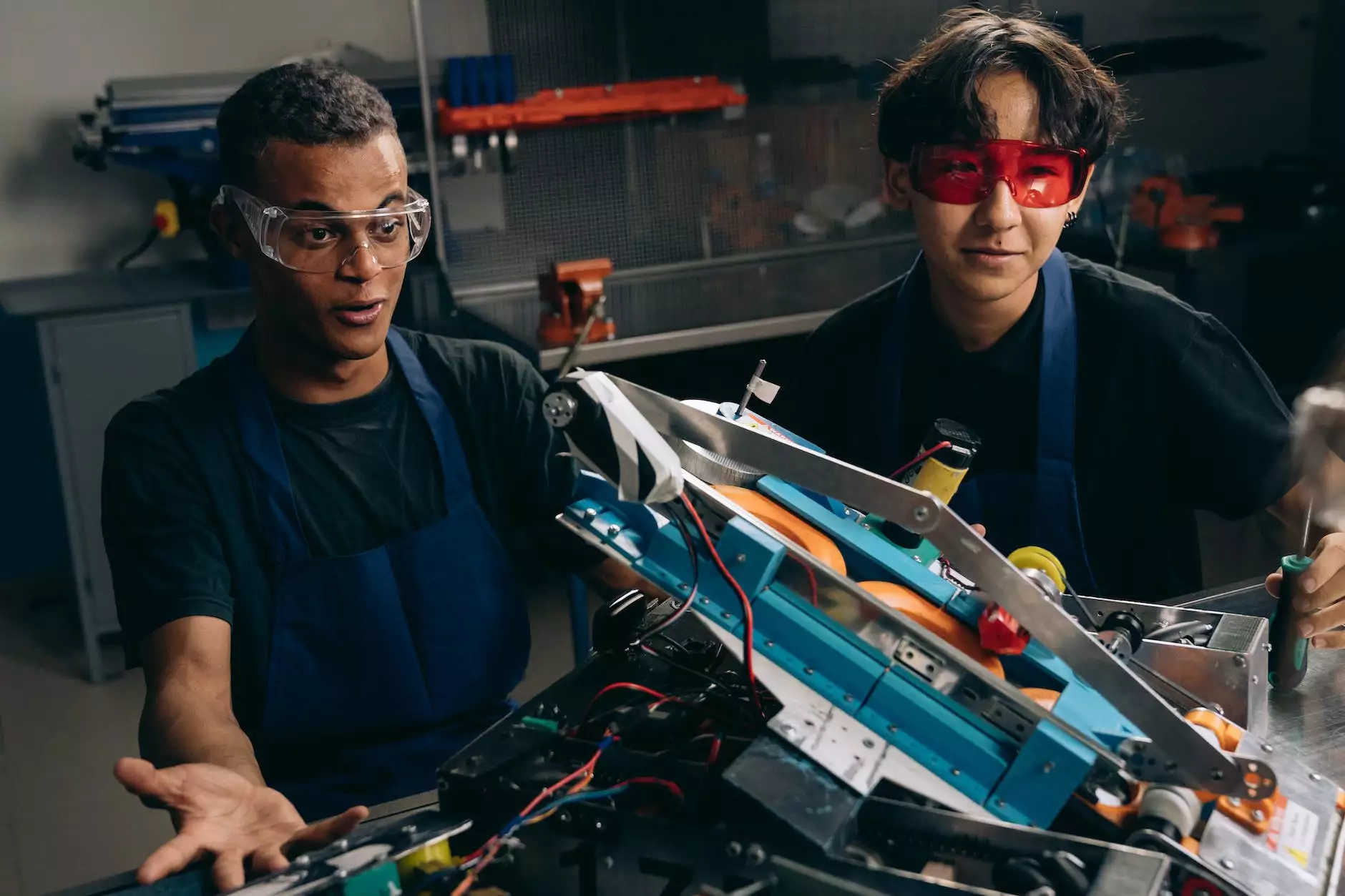
In the ever-evolving world of manufacturing, the term rapid prototyping has become synonymous with innovation and efficiency. This process allows businesses, particularly in metal fabrication, to create prototypes quickly and effectively—an essential step in refining products before they reach the final production stage. With the rise of digital technologies and advanced materials, rapid prototyping is reshaping how companies like Deep Mould engage with their market.
What is Rapid Prototyping?
Rapid prototyping is a group of techniques used to quickly assemble a scale model of a physical part or assembly using three-dimensional computer-aided design (CAD). The primary objective is to validate design concepts and functionalities visually and dimensionally. By employing various methods—including additive manufacturing (3D printing), CNC machining, and even advanced techniques like metal 3D printing—businesses can enhance product development cycles, reduce time-to-market, and lower costs significantly.
Key Benefits of Rapid Prototyping in Metal Fabrication
Utilizing rapid prototyping offers numerous advantages, particularly for businesses in the metal fabrication sector. Here are some of the critical benefits:
- Reduced Time to Market: By producing prototypes in a fraction of the time compared to traditional methods, companies can fast-track their innovations and gain a competitive edge.
- Cost Efficiency: Rapid prototyping minimizes material waste and labor costs, allowing for economically viable production processes without compromising quality.
- Enhanced Design Flexibility: Iterating on designs is more manageable and less costly, enabling engineers to play around with concepts and make necessary modifications swiftly.
- Improved Product Quality: Early-stage prototypes can be rigorously tested and evaluated for functionality, leading to higher quality and more reliable end products.
- Collaboration and Communication: Prototypes serve as tangible representations of ideas, facilitating better communication and collaboration among teams, stakeholders, and clients.
Rapid Prototyping Techniques
There are several prominent techniques used in rapid prototyping, each with its unique applications and benefits. Here’s an overview of the most common methods employed in metal fabrication:
1. 3D Printing (Additive Manufacturing)
3D printing is perhaps the most recognized form of rapid prototyping. It involves layering materials to build complex structures from CAD models. In metal fabrication, this can mean using advanced alloys to print functional parts directly.
2. CNC Machining
Computer Numerical Control (CNC) machining is a subtractive manufacturing process where material is removed from a solid block via rotating tools. This technique is ideal for creating high-precision prototypes quickly, making it invaluable for metal parts that require intricate designs.
3. Sheet Metal Fabrication
This technique involves cutting, bending, and assembling thin sheets of metal into functional prototypes. It is particularly useful for creating enclosures or framework models that require accuracy.
4. Stereolithography (SLA)
SLA is a 3D printing technique that uses a laser to cure resin into hardened plastic. It’s suitable for creating high-detail prototypes that can later be used for molds in metal casting.
5. Investment Casting
Investment casting, also known as lost-wax casting, is a method where a wax model is created, coated with a refractory material, and melted away to leave a cavity for molten metal. Prototypes created using this method can be very accurate and are often used in automotive and aerospace applications.
The Role of Rapid Prototyping in Driving Innovation
For businesses focused on metal fabrication, staying relevant means continuously pushing the boundaries of what's possible. Rapid prototyping serves as a pivotal tool in driving innovation by allowing companies to test new ideas without a significant upfront investment:
- Experimentation: Companies can experiment with new designs and materials without the commitment of mass production.
- Feedback Loop: Rapid prototypes can be presented to customers and stakeholders for valuable feedback, guiding future design iterations.
- Market Adaptation: Businesses can quickly adapt to changing market demands by rolling out enhanced prototypes tailored to customer needs.
- Customization: Customization of products becomes feasible and economically viable, meeting individual client specifications more effectively.
Implementing Rapid Prototyping in Your Metal Fabrication Business
To leverage the full potential of rapid prototyping, companies must adopt strategic implementations:
1. Invest in Technology
Acquisition of the latest 3D printing and CNC machining technologies is essential. Staying abreast of technological advancements ensures compliance with industry standards and market trends.
2. Training and Development
Training staff on how to utilize these advanced techniques and technologies enhances productivity. Knowledgeable employees can drive the prototyping process more efficiently.
3. Embrace a Culture of Innovation
Encouraging a forward-thinking environment where failure is viewed as a stepping stone can foster creativity, inspiring teams to push for innovative solutions.
4. Collaboration and Network Building
Collaborating with clients, suppliers, and industry peers can lead to shared knowledge and resources, enhancing the prototyping process and results.
Case Study: Success Stories in Rapid Prototyping
Many industry leaders have successfully implemented rapid prototyping to enhance their operations:
Example 1: Aerospace Industry Transformation
Companies like Boeing have utilized rapid prototyping to manufacture components efficiently, reducing the time taken in design iterations and improving precision.
Example 2: Automotive Innovations
Automotive giants like Ford and GM have embraced rapid prototyping whereby they can quickly produce prototype parts for testing, leading to enhancements in safety and performance.
Future Trends in Rapid Prototyping
As industries evolve, so too does the landscape of rapid prototyping. Here are a few trends shaping the future:
- Integration with AI: The incorporation of artificial intelligence in designing and optimizing prototypes is expected to accelerate development.
- Increased Material Options: Research is ongoing to develop new materials that can withstand various industrial applications, broadening the horizons for metal fabrication.
- Sustainability Focus: Future prototyping efforts will focus more on sustainable practices, including recycling materials and minimizing waste.
- Greater Customization Capabilities: Technologies will evolve to allow for individual customization at a larger scale without compromising efficiency.
Conclusion: Embrace the Future with Rapid Prototyping
In conclusion, the significance of rapid prototyping in the metal fabrication industry cannot be overstated. With its myriad benefits—from reducing time to market and costs to enabling innovation—this process is not just an operational tool; it’s a vital strategy for sustaining success in an increasingly competitive marketplace.
As more businesses understand the power of rapid prototyping, they must take the necessary steps to integrate these processes into their workflows. Embracing this approach will not only enhance product development but also ensure that companies remain at the forefront of their industries.