The Benefits and Applications of Extrusion Moulding in Modern Business
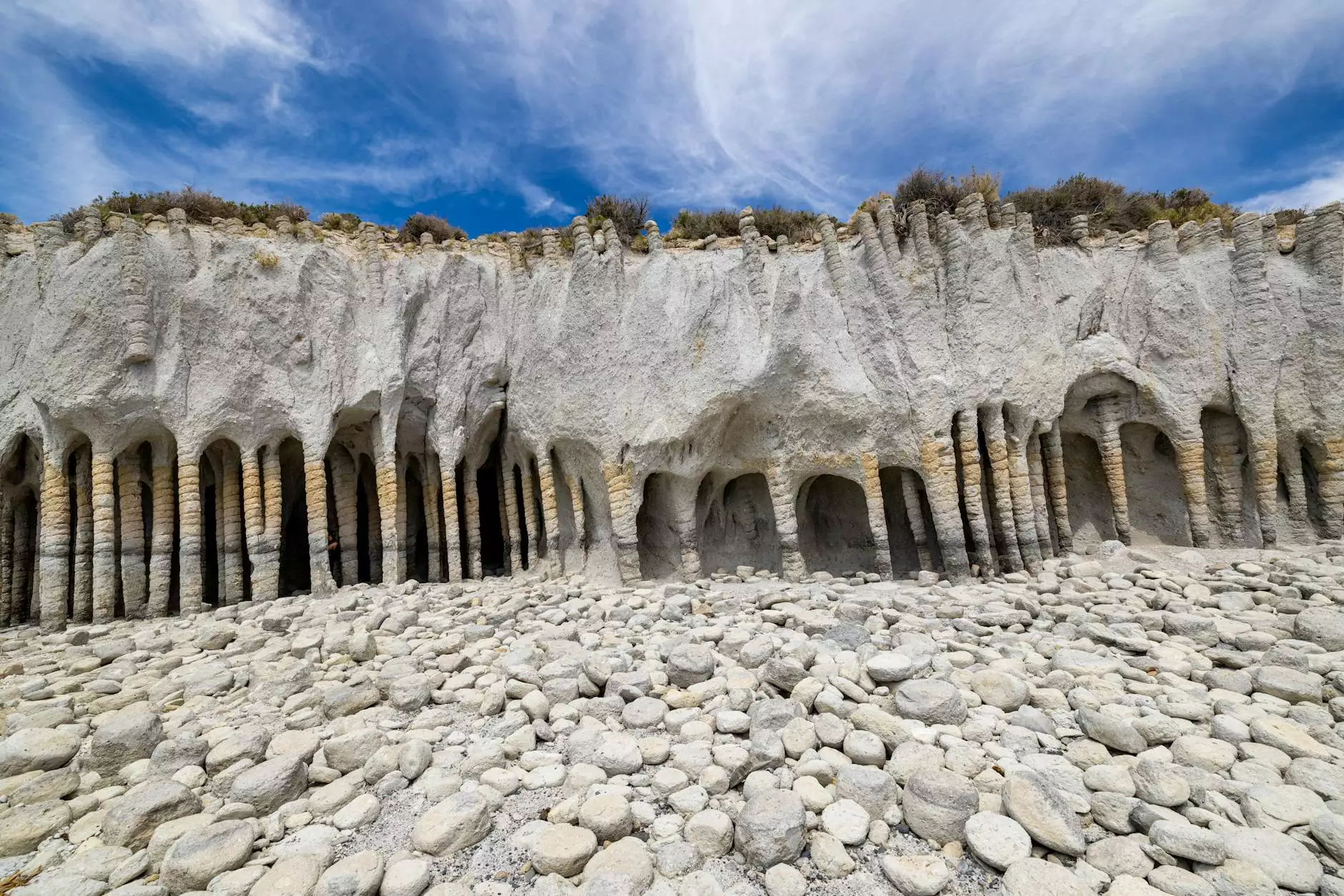
In today's dynamic business environment, extrusion moulding has emerged as a crucial process that significantly influences multiple industries, including art supplies, product design, and 3D printing. This article delves into the intricacies of extrusion moulding, outlining its definition, its multifaceted applications, and its transformative impact on various sectors.
Understanding Extrusion Moulding
Extrusion moulding is a manufacturing process in which material is pushed through a die of a particular cross-section to create long shapes or parts. This method is widely employed in the production of plastic components, but it also finds a place in the processing of metals, food, and other materials.
The process involves several key steps:
- Feeding: Raw material (primarily in pellet form) is fed into the extruder.
- Melting: The material is heated until it becomes a molten fluid.
- Extruding: The molten material is forced through a die, shaping it into the desired form.
- Cooling and Solidifying: The shaped material is cooled to solidify its form, often using air, water, or other cooling methods.
- Cutting: Finally, the extruded product is cut to length before further processing or packaging.
The Importance of Extrusion Moulding in Business
Extrusion moulding holds great significance in business for several reasons:
- Cost-effectiveness: The efficiency of the extrusion process reduces material waste, which contributes to lower production costs. This efficiency is critical for businesses aiming for high-volume output.
- Versatility: This technique can handle a wide array of materials, including thermoplastics, metals, and food products, making it applicable across various industries.
- Consistency: Extrusion moulding provides uniformity in the product dimensions and quality, ensuring that every batch meets stringent manufacturing standards.
- Complex Geometries: Complex shapes can be achieved through specific die designs, allowing businesses to innovate without the constraints of traditional manufacturing methods.
Applications of Extrusion Moulding
1. Art Supplies
In the realm of art supplies, extrusion moulding plays a pivotal role by enabling the production of various tools and materials. Here are some examples:
- Colored Pencils: The process is commonly used to create the cores of colored pencils, where the consistent extrusion ensures uniform color application.
- Plastic Brushes: Brushes with precision-engineered handles and bristles are produced through extrusion, ensuring durability and functionality.
- Canvas Stretchers: Lightweight yet strong plastic stretchers for canvases can be produced with advanced extrusion moulding techniques.
2. Product Design
In product design, extrusion moulding contributes significantly to the efficiency and aesthetics of products:
- Consumer Electronics: From casings to internal components, many electronic devices utilize parts made from extruded materials, ensuring both functionality and style.
- Automotive Components: Various lightweight parts, from clips to seals, benefit from the strength and precision that extrusion offers.
- Packaging Solutions: Extruded materials are frequently used to create innovative packaging designs that enhance product protection and shelf appeal.
3. 3D Printing
Innovative uses of extrusion moulding are also taking shape in the burgeoning field of 3D printing:
- Filament Production: The production of 3D printing filaments, such as PLA or ABS, often involves extrusion, providing quality material that is critical for successful printing.
- Complex Structures: Advances in extrusion methods are allowing for the creation of intricate designs that can be printed layer by layer, significantly enhancing the capabilities of 3D printing technology.
- Sustainable Materials: Innovations in extrusion are leading to the production of biodegradable and eco-friendly filaments, aligning with the growing demand for sustainable practices in manufacturing.
Benefits of Adopting Extrusion Moulding
Business owners and manufacturers are increasingly recognizing the numerous benefits of adopting extrusion moulding:
- Increased Productivity: The continuous nature of the extrusion process reduces cycle times, enabling manufacturers to scale production efficiently.
- Material Savings: Reduced waste during manufacturing not only lowers costs but also contributes to environmental sustainability.
- Customization: Custom dies can be created for specific applications, allowing companies to respond quickly to market trends without significant lead times.
- Enhanced Performance: Parts produced through extrusion can often exhibit superior mechanical properties, improving the overall quality and lifespan of the products.
Future of Extrusion Moulding in Business
As industries evolve, the future of extrusion moulding looks promising, driven by technological advancements and market demands:
With the rise of additive manufacturing, companies will likely witness a blending of traditional extrusion methodologies with contemporary techniques, fostering innovation and driving efficiency. Furthermore, sustainable materials are expected to proliferate in the realm of extrusion, leading to increased interest in eco-friendly manufacturing practices.
Innovations to Watch
In the coming years, several innovations in extrusion moulding may transform its applications:
- Smart Manufacturing: The integration of IoT and AI into extrusion processes could lead to real-time monitoring and adjustments, significantly enhancing quality control.
- Advanced Materials: The exploration of new composite materials that can be extruded promises not only stronger products but potentially lower production costs.
- Automation: As production demands increase, automation in the extrusion process will likely streamline operations, enhancing overall productivity.
Conclusion
Extrusion moulding is a game-changer for businesses in art supplies, product design, and 3D printing. Its numerous advantages, from cost efficiency to versatility, make it an invaluable manufacturing process in the modern marketplace. As industries continue to innovate, the ongoing evolution of extrusion moulding will undoubtedly play a crucial role in shaping the future of manufacturing and product development.
As you explore the potential of extrusion moulding, consider how it can elevate your business offerings and meet the ever-changing needs of today's consumers. For further insights and products, visit arti90.com.